Challenges related to the decontamination of post-consumer and residual materials
Contamination of recycled polymers
As explained in the chapter on supply, once you have selected the materials respecting your charter, this materials will usually be contaminated.
This is particularly the case for post-consumer and residual materials.
This contamination comes from multiple sources. The majority of post-consumer and residual plastics are made up of plastic containers and packaging that often retain remains of their contents (food, detergents, cosmetics, oils...). Besides, at the end of their life, they end up in a recycling bin and then in a sorting center where they suffer other types of cross-contamination (other types of plastics, paper, metal or wood shavings, textile fibers, sand, dust, etc.)
Below is an image of the contents of the recycling bins upon arrival at a sorting centre.

Problems due to residual contamination of plastics
Although our sorting centers do a remarkable job of sorting and separating materials, it is almost impossible to eliminate all contamination at this stage. Therefore it is not uncommon for the plastic bales supplied by sorting centers to still have more than 15% residual contamination.
This residual contamination can cause several problems both in terms of quality and performances of the finished product as well as in terms of production equipment efficiency.
These contaminants can also cause problems for workers health and environmental protection.
Below is an example of an HDPE plastic bale, as sold by a sorting centre, where you can already see some contaminants like paper labels.
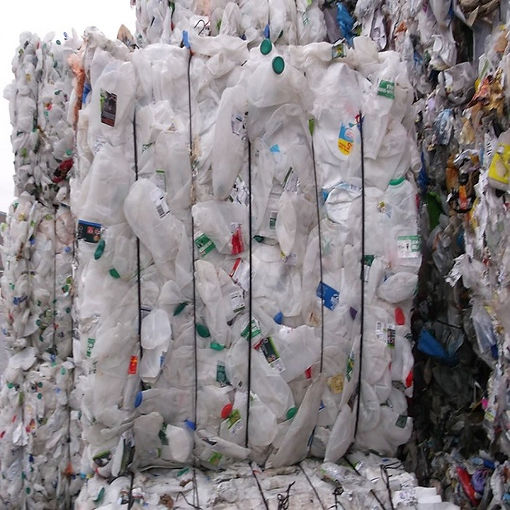
Decontamination solutions and technologies
Manufacturers who wish to use recycled materials must therefore eliminate their residual contamination or at least reduce its impacts. Fortunately there are technologies and industrial equipment able to remove contaminants from recycled polymers.
Example:
-
Elimination of humidity and volatile substances by drying at low temperature (60-80°C)
-
Removal of solid contaminants by solid/liquid filtration:
Screen-Changer Technology
-
Elimination of compounds and organic substances (oils, greases...) by vaporization/aspiration:
Degassing technology
Below are some examples of plastic packaging and decontamination equipment (washing line, screw washing line, grinder, screen-changer, degassing line).
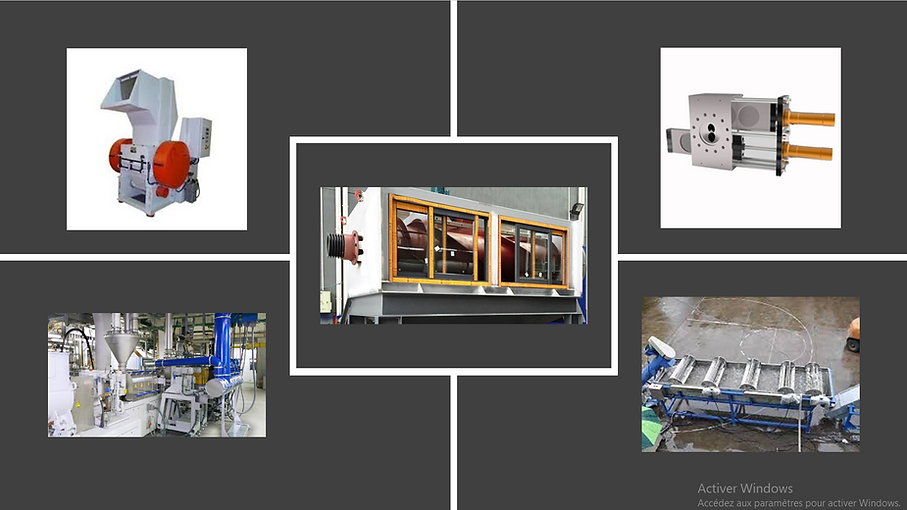
Efficiency of decontamination technologies
Unfortunately, and contrary to what some suppliers claim, there is no universal decontamination technology or equipment.
IIndeed, although technologies continue to improve, there is none that can fully decontaminate plastics. In addition, their efficiency remains relative and depends on several factors including:
-
The type of plastic to be decontaminated.
-
The type of contaminants to be removed.
-
The initial contaminant concentration.
-
Your production rate.
Just because a piece of equipment performs well with certain types of materials at a given production rate, does not mean that this will be true once this piece of equipment is integrated into your plant.
Manufacturers primarily want to sell their equipment so they will usually tell you what you want to hear. It's normal they play their role. But be careful, once you have purchased the equipment you are responsible for it and will have to bear the consequences of any failures and these can be severe, particularly because of the paradox of industrial decontamination.
Before you let yourself be convinced by the performance of a decontamination technology, let our experts ensure that it meets your expectations. This can save you a lot of problems that we will discuss in the next chapter.
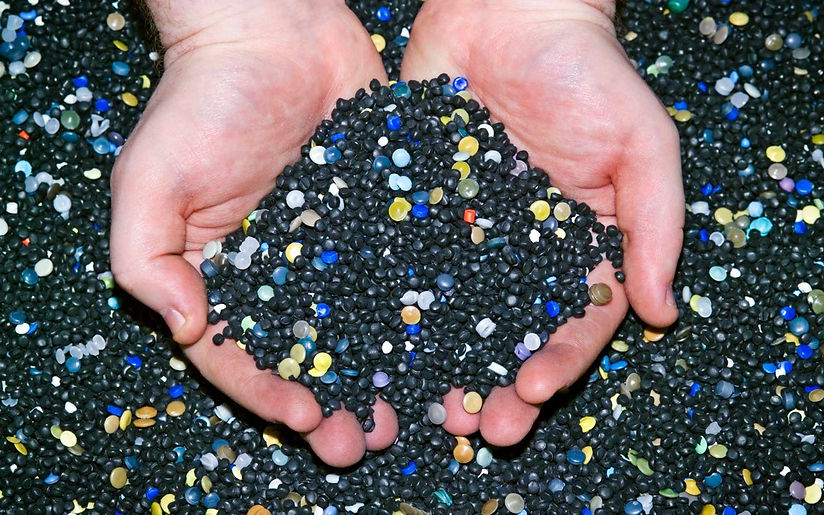
The "paradox" of industrial decontamination
Industrial decontamination produces a great paradox.
Indeed, decontaminating consists of extracting the contaminants present in the raw materials.
But it does not stop there. Because once you have successfully extracted these contaminants, you must now ensure that they are managed and treated in a safe and environmentally friendly way.
The more you decontaminate, the greater the risk that your plant will become itself a source of contamination.
This is particularly true for volatile contaminants, which, as their name suggests, spread easily in the environment, posing a risk to both the environment and the health of plant workers. We are talking here, among other things, about vapours, fumes and fine particles that are released during decontamination operations.
The same also applies to treatment water, particularly washing water, if your decontamination operations include a washing and drying step for the materials. You will need to find out about the maximum level of contamination that your city or municipality tolerates in its sewage system and comply with it at all costs.
The same applies to the maximum levels of volatile contaminants (chemical compounds, fine particles, dust) accepted by health authorities in work environments and comply with them.
This is all the more true since the washing and decontamination operations most often involve a grinding operation which generates dust and fine particles.
This translates into the decontamination paradox that:
“The more you decontaminate, the more contamination problems you will have to manage”.
“The more you decontaminate, the more you will have to interact with the authorities for the workers health and environment protection. »
All the companies that underestimated this reality unfortunately had to, at the request of the authorities, cease their activities. Activity can theoretically resume once the company has successfully complied to the required standards, but many of them have never recovered.
The challenges related to the decontamination of materials can therefore have serious consequences and for this reason it is necessary to demonstrate great expertise in the choice of technologies and equipment to be acquired in this area.
Our team of experts will enable you to meet these challenges and guarantee the profitability and success of your business.
